BOOST PRODUCTIVITY WHILE LOWERING COSTS AND ENVIRONMENTAL IMPACT
As part of our continuous improvement process, we design upgrades to help our customers to improve the performance of their machines, reduce cost of ownership, and reach their sustainability goals.
- Protecting equipment performance
- Minimising the total cost of ownership
- Environmental Upgrades
PROTECTING EQUIPMENT PERFORMANCE
Upgrades designed to improve your machine performance and boost the productivity of your operation
On-tool particle-reduction upgrades for Maglev Turbopumps
In our ongoing mission to improve our customers’ productivity and yield, we devised a series of solutions that enable our customers to reduce on-wafer particle contamination in semiconductor applications by using three on-tool technologies, our Anti-Recoil Technology, a Rotor Cup Cover, and the use of High Temperature Pumps.
Anti-Recoil Technology
During production, particles can recoil from the turbopump into the chamber, potentially contaminating the wafers and reducing productivity. Our Anti-Recoil technology significantly reduces particle contamination by letting them pass easily through the turbo pump into the exhaust.
Rotor Cup Cover
To prevent corrosion and particulate build up on the rotor cup (at the inlet of the turbo pump), we developed a corrosion resistant Rotor Cup Cover that prevents both the formation of deposition and the corrosion of the stainless steel-components.
High Temperature Pumps
Another source of particle contamination comes from deposition inside the turbo pump, which can also allow particles to travel back through the turbo pump and into the chamber. By using High Temperature Pumps the gas path is heated up to extremely high temperatures lessening the formation of deposition. These pumps have a special high heat emissivity coating on key vacuum components, such as the rotor and stator, and their temperature profile is continuously optimised for best results.
All three particle reduction technologies can be installed during a regular pump service at our Service Technology Centre to ensure customers can optimise productivity for new equipment and their existing installed base.
Improve semiconductor yield with EUV Pump Upgrades
In the competitive industry of semiconductor manufacturing, maximising productivity while managing energy costs in manufacturing facilities is crucial. Our EUV dry pump upgrades are designed to significantly enhance the performance of your equipment, ensuring optimal semiconductor yield improvement. By integrating advanced semiconductor equipment services, our upgrades not only boost yield in semiconductor manufacturing but also contribute to substantial energy savings. This holistic approach to yield improvement in semiconductor processes ensures that your manufacturing facilities operate at peak efficiency.
XCEDE Dry Pump protection for harsh manufacturing processes
The XCEDE’s Dry Pump protection technology prevents the corrosion of critical pump components and increases the meantime between service intervals, maximising costumer uptime. This technology outperforms all competing methods by using a complex combination of surface treatment and precision engineering to reduce the chemical and mechanical wear within the pump mechanism for Edwards iH, iXH and iXM pump families.
MINIMISING THE TOTAL COST OF OWNERSHIP
Upgrades designed to increase the meantime between service and increase the efficiency of your equipment fleet for a reduced Total Cost of Ownership.
Abatement Porous Head
Edwards developed the Porous Head, a field service upgrade that employs a sintered, porous, metal block, which evenly spreads an air purge across the surface to reduce the risk of powder accumulation. It replaces the traditional ceramic insulator head.
During the abatement process, solids, typically powders, can build up in unwanted areas of the system, such as the underside of the inlet head. This powder accumulation leads to a blockage that prevent the flow of process gases, causing frequent planned service interventions. In one year of severe processes, this powder build-up can cause more than nine service interruptions resultings in increased cost of ownership through labour and spare parts usage.
Customers using the Porous Head upgrade, have moved from ten service intervals per year to just two on average. This has removed an average of 64 hours of tool downtime per year for customers without a backup abatement system, resulting in $1.5million of additional throughput.
Customers with a back-up abatement system see substantial savings in spare parts, maintenance labour, and increased energy efficiency by reducing their dependency on their back up system.
Life Services
Fleets with machinery that has been in use for more than five years risk unexpected failures in their critical electronics regardless of their mechanical performance, which is mainly preserved by effective maintenance regimes.
Edwards Life Services solution is a great option to refresh machinery and extend your fleet's lifetime. Life Services covers all the major system electronic parts with extended warranties, keeping your equipment running for years to come.
Life Services is available through our global network of Service Technology Centres.
ENVIRONMENTAL UPGRADES
Upgrades designed to increase the lifetime of your equipment fleet and its environmental impact to help you reach your sustainability targets.
Reducing energy costs in manufacturing with our energy saving upgrades
This Edwards dry pump upgrade of the iXH1210 is an easy swap out, with no additional work for onsite teams and no downtime loss during the upgrade process.
It delivers almost a third off your energy costs to run, and helps to mitigate your environmental impact, by saving more carbon emissions, contributing to your environmental goals. No wonder we call it the energy saving upgrade.
Now imagine multiplying those numbers by the number of pumps that can be upgraded in your Fab?
Also, there is the additional benefit that our customers do not need to plan capital for new pumps, as the upgrade can be achieved through the Edwards Intelligent Service upgrade process.
EUV energy saving pump upgrade
In semiconductor manufacturing, sustainability is becoming increasingly vital. Our EUV dry pump upgrades are engineered to support sustainability by significantly reducing energy consumption in EUV processes and EUV power consumption. By upgrading your pumps, you can optimise the energy performance of the process, achieving substantial energy savings while boosting productivity.
Learn more about EUV energy saving in our customer success story below:
Heat Exchangers
Fab-wide cooling water contamination is a risk posed by abatement systems without rigorous maintenance schedules. In many systems, heat exchangers are vulnerable to corrosion damage from acidic process chemistry that can cause a leak into the Fab’s process cooling water. This contamination can damage other process tools that use the same cooling water circuit. It also poses a risk to the environment as it is hazardous to dispose of.
The heat exchanger field service upgrade kit is an effective solution that converts the existing brazed heat exchanger into a new plate and gasket design, without significant modification to the system. It provides improved resistance to acid attack when compared with original heat exchangers, offering an enhanced service life of around five to ten times and reducing the risk of Fab cooling water contamination.
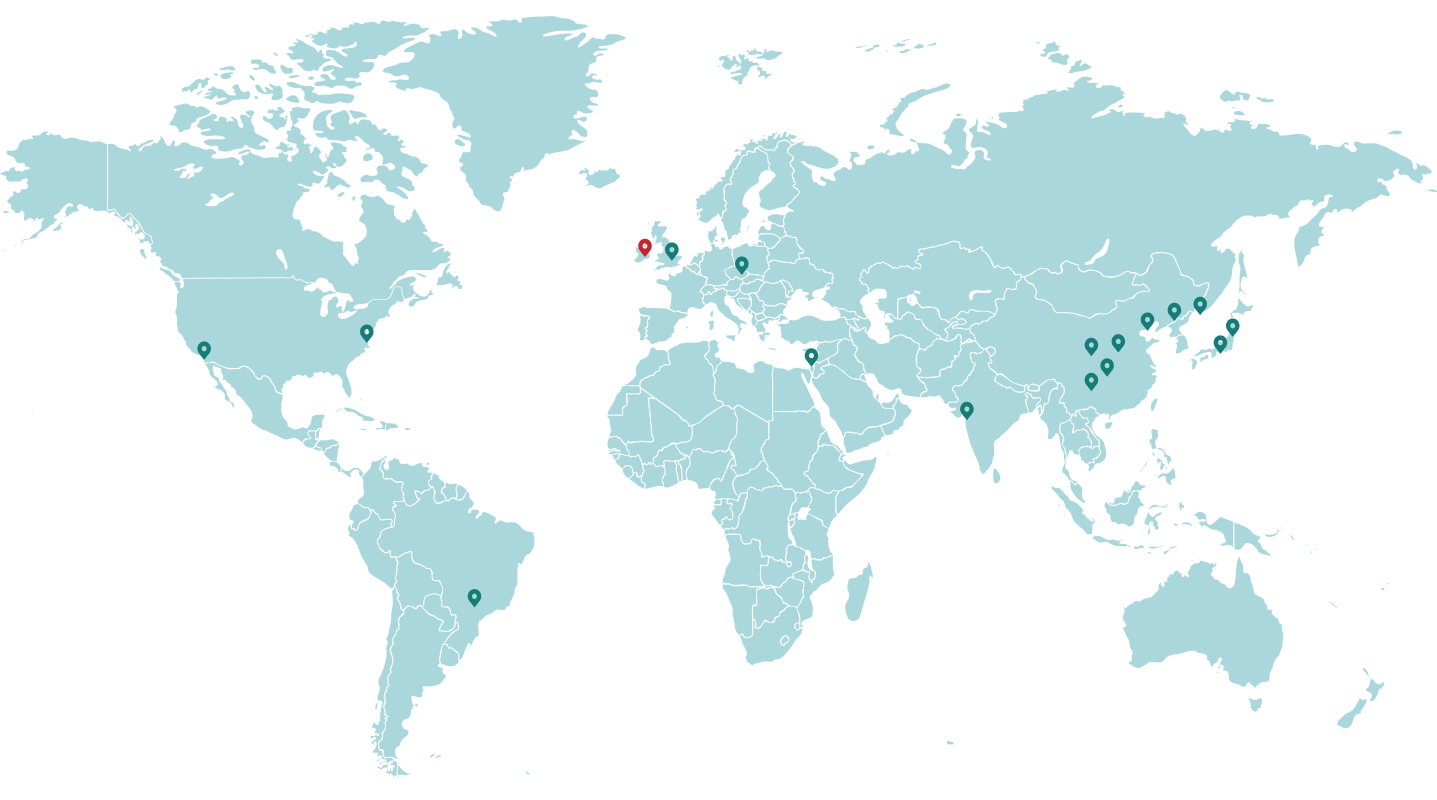