RESTORE EXISTING VACUUM AND ABATEMENT EQUIPMENT PERFORMANCE WHILE SAFEGUARDING THE ENVIRONMENT
We offer a variety of remanufacturing services to meet your specific goals, whether that is enhanced reliability, boosted equipment performance, or improved efficiency that impacts your total cost of ownership. We only use Edwards genuine parts in repairs. We inspect, build and test pumps to factory -derived standards and processes, ensuring that our world-class quality is delivered no matter which service solution you choose.
All our service operations are conducted at the highest international standards in accordance with ISO9001 (Quality), ISO14001 (Environmental), and OHSAS18001 (Workplace safety).
- Standard Services
- Exchange
- Certified Products
STANDARD SERVICES
Your uptime is extremely important, and the reliability of your vacuum pumps is crucial to maintain it. To ensure your pump remains reliable throughout its operating life, a solid maintenance regime is required to deliver the performance you need, when you need it.
Depending on your vacuum application, the intensity of the service events can be very different. Our ability to service your pump using factory derived standards and processes will give significant benefits in its reliability. However, we also recognise that not every process is the same and sometimes more economic solutions are required.
We have serviced hundreds of thousands of vacuum pumps and understand how they have been manufactured and used. Based on this experience, we have developed a suite of service products so that you can be sure that you get maximum reliability, whilst keeping the total cost of ownership to a minimum.
EXCHANGE
Exchange encompasses a completely rebuilt and tested unit for the purpose of immediate swap out, usually available for dispatch within 24-48 hours of the acceptance of the customer’s purchase order. After swapping the pump at the customer’s site, the replaced unit must be returned to our Service Technology Centres for repair. All service exchange rebuilds are carried out using Edwards genuine spare parts, ensuring world class quality and reliability. Further accessories can be added to achieve a specific configuration, though these may incur additional charges and extended turnaround times.
Most Exchange products are available as emergency product replacements which are available off the shelf for immediate shipment. This service provides the fastest possible replacement for minimal process disruption.
CERTIFIED PRODUCTS
To reduce capital expenditure, certified products are a cost effective and environmentally sustainable alternative to purchasing new equipment.
These are pre-owned units, fully serviced using exclusively genuine Edwards parts, ensuring the quality, reliability, and performance of your equipment. Certified products are provided with all the accessories required to install the product straight out of the box. Typical installation accessories include electrical connectors, water connectors, inlet and exhaust O-rings, and full instructions for installation and usage.
Many new products are also available as Certified. Tested and rebuilt to factory derived standards, they offer a cost-efficient way to expand pumping capacity, or to replace existing equipment without the need to re-qualify. All Certified products have carefully repurposed Edwards genuine parts, reducing their overall environmental impact.
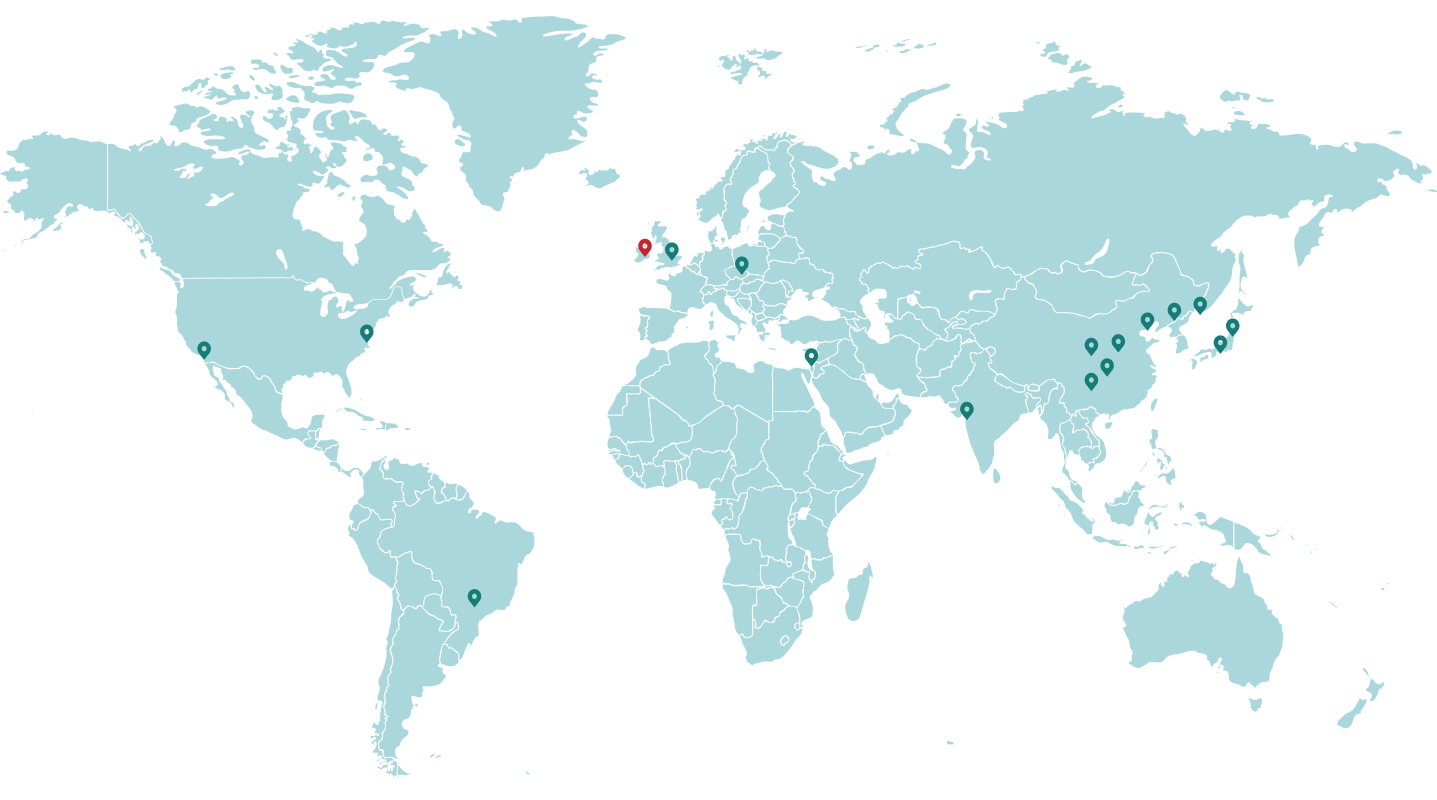